Joseph Blake Water Treatment Plant Phase 1A Improvements
Location
Highlands Ranch, ColoradoValue
17MDelivery Method
- Design-Bid-Build
Client Type
MunicipalProject Type
- Plant
In Highlands Ranch, Colorado—a Denver suburb of over 100,000 residents—water demands required essential upgrades to the Joseph Blake Water Treatment Plant (WTP) to maintain reliable service for the community. Centennial Water & Sanitation District (CWSD) selected Garney to lead Phase 1A of the plant’s rehabilitation, focusing on modernizing the pretreatment process.
Garney installed ten additional flocculators across the two raw water intake trains, improving particle collisions and forming larger flocs as water enters the sedimentation basins. The team also replaced outdated tube settlers with advanced plate settlers to enhance sedimentation, providing increased surface area for greater efficiency. These upgrades boosted the plant’s capacity and improved water quality during pretreatment.
The team navigated the challenges and complexities of working within an existing operational plant throughout the project. Seasonal water demand shaped the project timeline, requiring the plant to stay fully operational during warmer months to meet increased usage. During cooler months, the plant still needed to maintain partial operations, so only one sedimentation basin and train could be taken offline at a time to install new flocculators and plate settlers. Despite the limited window for completion, the team worked efficiently to deliver the project on time, avoiding any delays in the installation. The team also faced access challenges while upgrading the system within an existing structure. Concrete pumping and equipment installation had to be done through holes cut into the roof, requiring extensive coordination and planning with the Mechanical Superintendents to ensure safe and efficient operations.
After completing the first train, the team experienced an unexpected delay in receiving new electrical gear. To maintain operations during the cooler months, they collaborated with electricians to install variable-frequency drives in the plant’s motor control center. This temporary solution allowed the upgraded train and flocculators to run on the old electrical system until the new gear arrived.
The project enhancements improved efficiency and delivered cleaner, higher-quality water to the community. Turbidity levels leaving the pretreatment basins fell from an average of 1.0-2.0 Nephelometric Turbidity Units (NTU) to less than 0.5 NTU despite nearly doubling the flow rate compared to the old system. The total pretreatment capacity increased from 26 million gallons per day (MGD) to 44 MGD. The higher quality water leaving the pretreatment system has significantly improved filter runtimes.
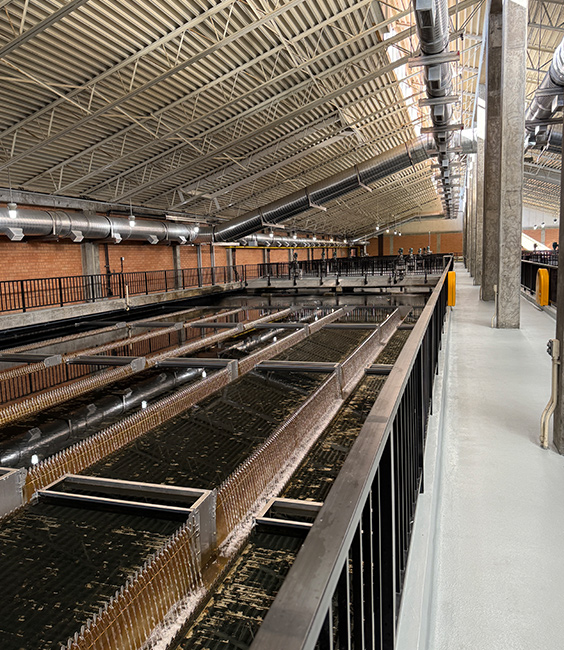
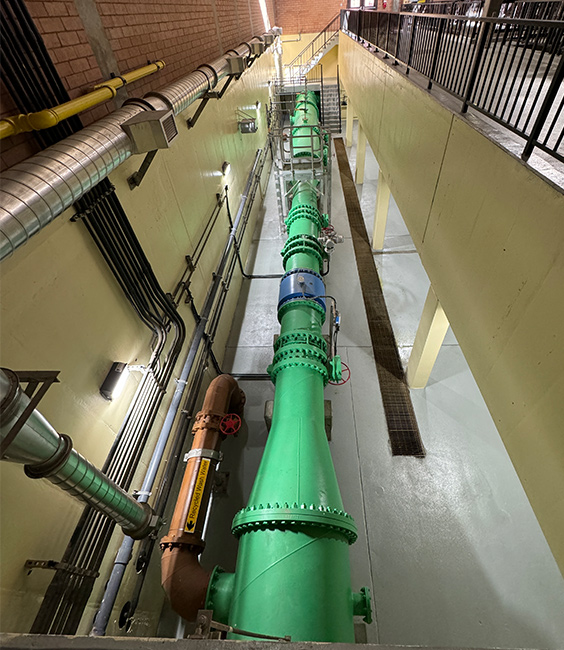
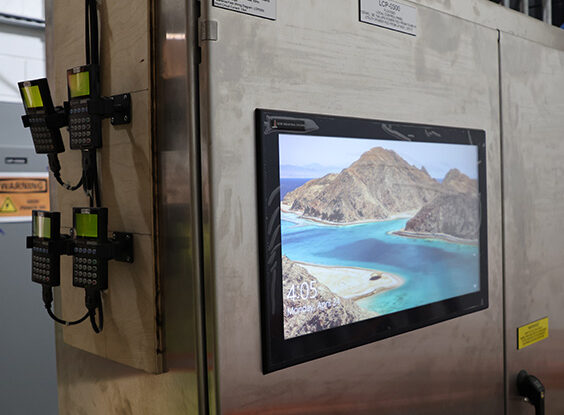
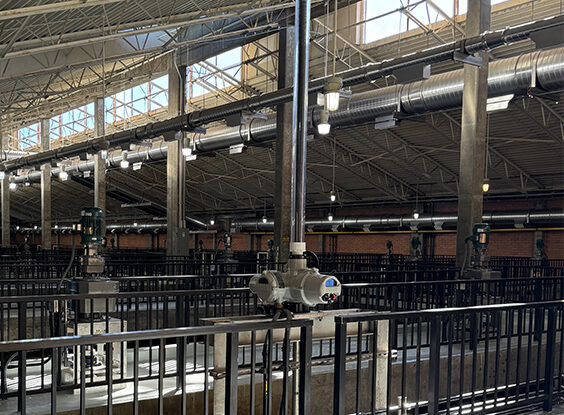
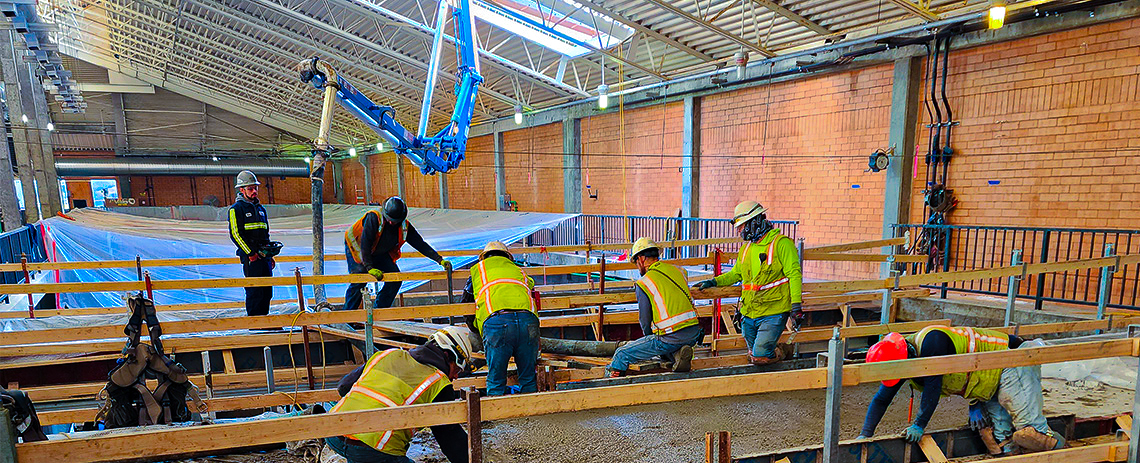
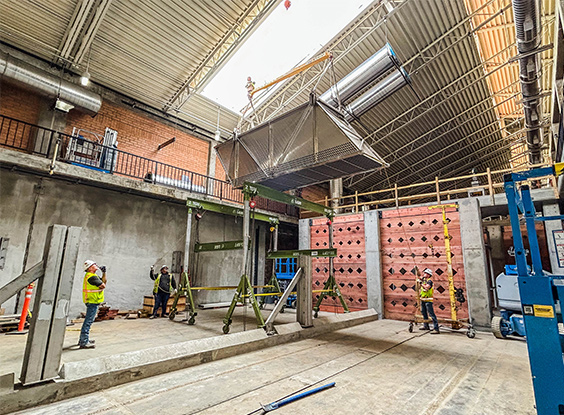
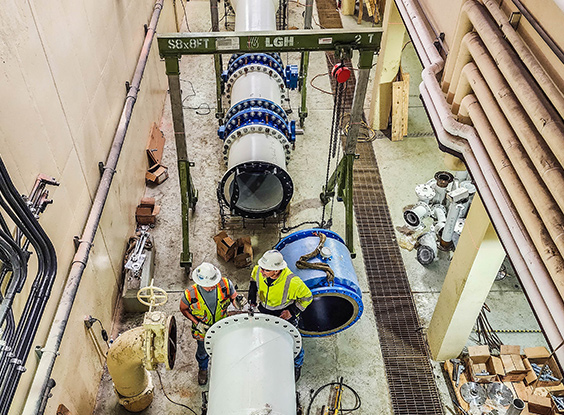